3月3日09時(shí)09分,陸豐核電5號(hào)機(jī)組SG隔間鋼板混凝土結(jié)構(gòu)模塊3順利吊裝就位,標(biāo)志著三個(gè)SG模塊在保障安全質(zhì)量可控的前提下全部實(shí)現(xiàn)高效精準(zhǔn)吊裝,為后續(xù)5號(hào)機(jī)組穹頂?shù)跹b重要節(jié)點(diǎn)創(chuàng)造了有利條件。
SG隔間模塊是反應(yīng)堆廠房中蒸汽發(fā)生器(英文簡稱SG)房間的內(nèi)部結(jié)構(gòu),底部位于核島廠房內(nèi)部結(jié)構(gòu)+17.5米板,頂標(biāo)高+32.2米,由鋼板、預(yù)埋件及鋼筋等組成,模塊呈現(xiàn)“U”字型,共包含3個(gè)模塊。
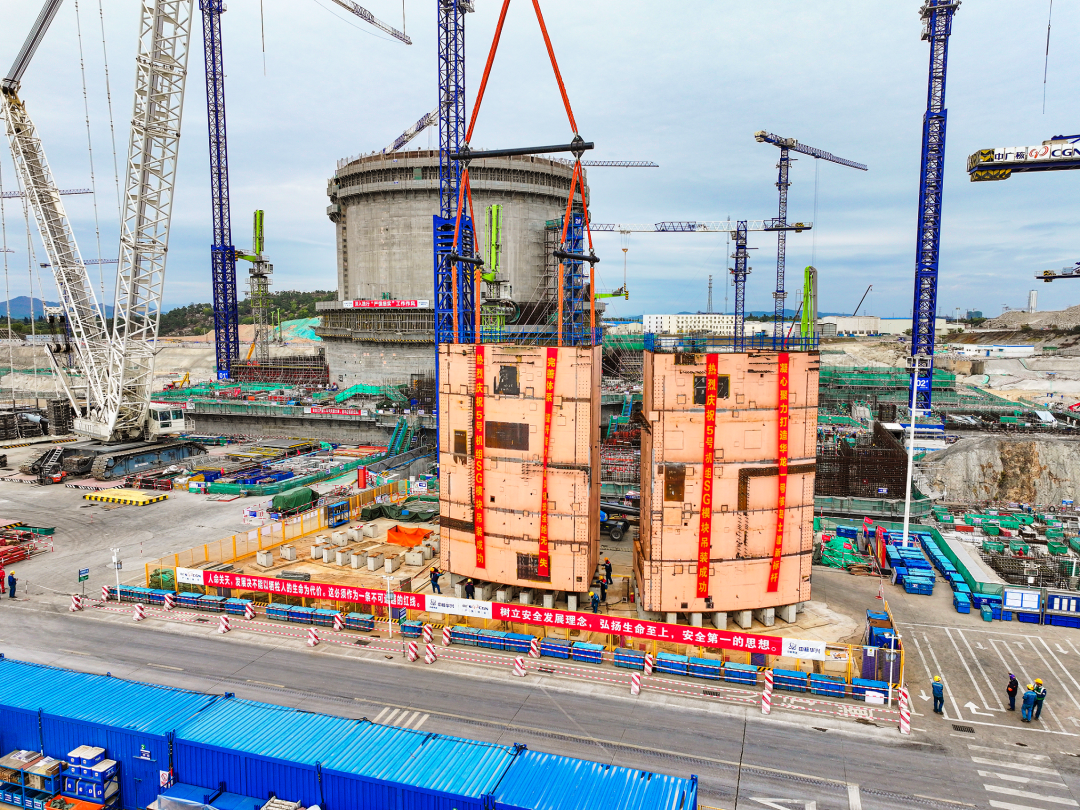
為將陸豐核電項(xiàng)目打造成為華龍一號(hào)建設(shè)標(biāo)桿,項(xiàng)目管理大團(tuán)隊(duì)始終堅(jiān)持把創(chuàng)新作為引領(lǐng)發(fā)展的第一動(dòng)力,一體推進(jìn)先進(jìn)建造技術(shù)、施工邏輯優(yōu)化、數(shù)字化轉(zhuǎn)型和微創(chuàng)小改,以創(chuàng)新賦能項(xiàng)目建設(shè)。項(xiàng)目團(tuán)隊(duì)秉持“應(yīng)模盡模、未模創(chuàng)模”的理念,在吸取和借鑒同行項(xiàng)目經(jīng)驗(yàn)的基礎(chǔ)上,推進(jìn)5號(hào)機(jī)組內(nèi)部結(jié)構(gòu)SG 隔間由鋼板混凝土模塊化施工技術(shù)替代原有的鋼筋混凝土結(jié)構(gòu),即SG 隔間模塊化施工技術(shù)。
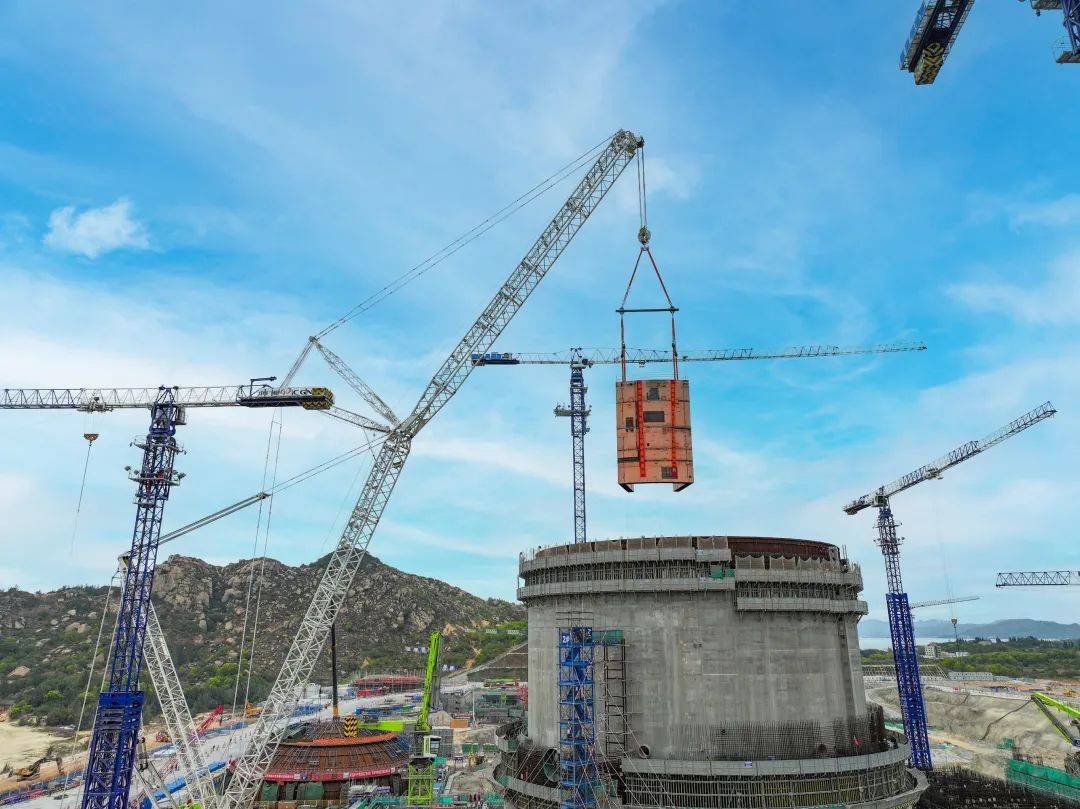
該技術(shù)采用廠外集約化車間預(yù)制分塊加工,然后運(yùn)送至項(xiàng)目施工現(xiàn)場(chǎng)拼裝,最后一次性整體吊裝就位。相較于傳統(tǒng)鋼筋混凝土結(jié)構(gòu),可以減少鋼筋綁扎、支模等工序,實(shí)現(xiàn)平行施工,避免多專業(yè)交叉施工,改善作業(yè)環(huán)境,優(yōu)化人力投入,降低安質(zhì)環(huán)管理風(fēng)險(xiǎn),提升施工精度和施工質(zhì)量,可實(shí)現(xiàn)內(nèi)部結(jié)構(gòu)主關(guān)鍵路徑工期優(yōu)化約20天。
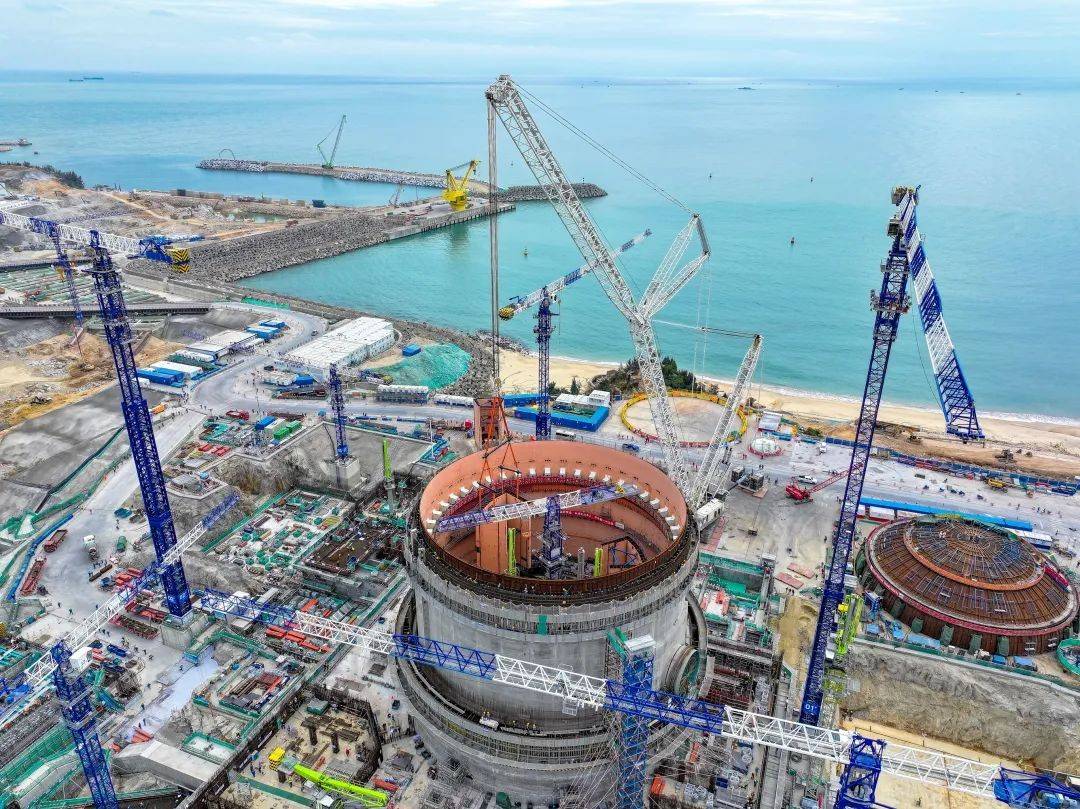
SG隔間單個(gè)模塊平面尺寸為10.5m×8.3m×14.7m,凈重159.9噸,吊裝總重量約190.5噸,模塊吊裝工藝精度要求高、安全就位難度大。為確保一次順利吊裝到位,項(xiàng)目管理大團(tuán)隊(duì)堅(jiān)持前瞻性思考、系統(tǒng)性謀劃,對(duì)吊裝的各個(gè)環(huán)節(jié)和控制措施進(jìn)行科學(xué)分析,多次召開專題推進(jìn)會(huì),梳理先決條件,進(jìn)行施工方案交底和安全技術(shù)交底,精心組織全過程模擬推演,抓實(shí)抓細(xì)責(zé)任落實(shí)和資源調(diào)配,推進(jìn)前后臺(tái)密切配合、高效聯(lián)動(dòng),確保吊裝節(jié)點(diǎn)順利實(shí)現(xiàn),安全質(zhì)量萬無一失。3月2日早上7點(diǎn),陸豐核電5號(hào)機(jī)組項(xiàng)目施工現(xiàn)場(chǎng)天氣晴朗,風(fēng)速平穩(wěn),SG隔間模塊吊裝正式開始。經(jīng)歷起鉤、變幅、回轉(zhuǎn)、落鉤、就位等一系列動(dòng)作,耗時(shí)26小時(shí)10分,3個(gè)SG隔間模塊高質(zhì)量吊裝就位。
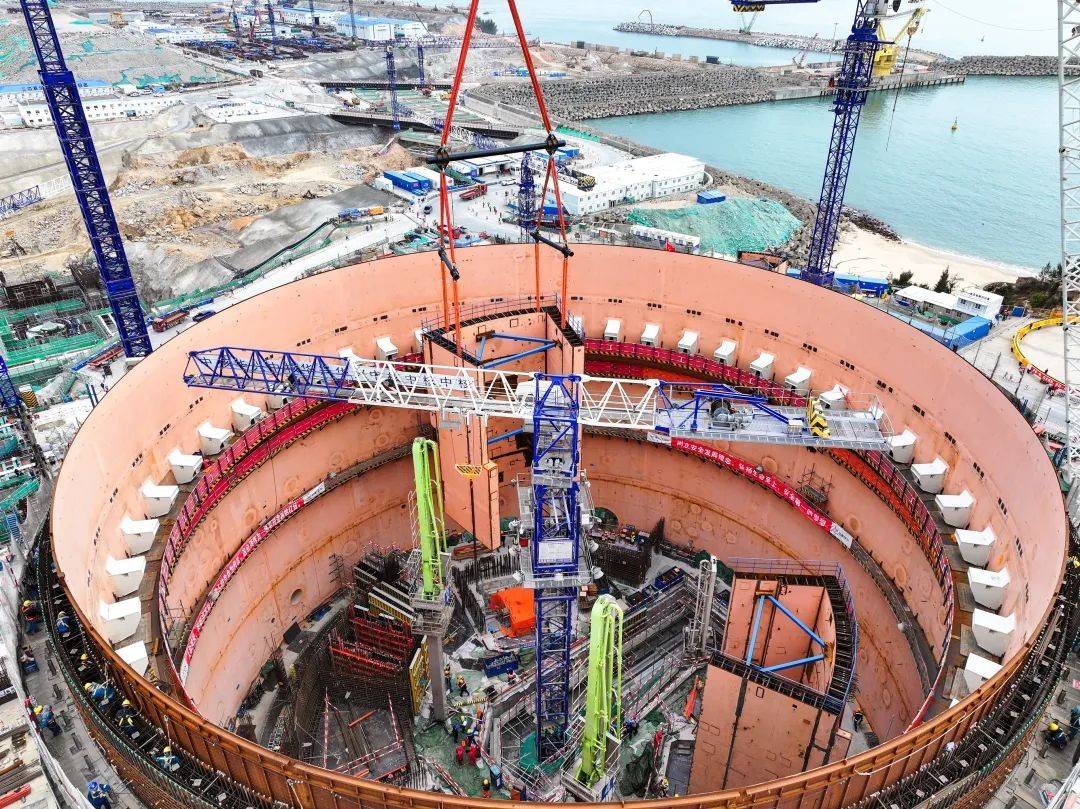
5號(hào)機(jī)組核島SG隔間模塊的順利吊裝,為后續(xù)穹頂?shù)跹b奠定了堅(jiān)實(shí)的基礎(chǔ)。后續(xù),陸豐核電將繼續(xù)完整、準(zhǔn)確、全面貫徹新發(fā)展理念,統(tǒng)籌高質(zhì)量發(fā)展與高水平安全,深入踐行“嚴(yán)慎細(xì)實(shí)”工作作風(fēng),大力弘揚(yáng)陸核精神,抓住科技創(chuàng)新這個(gè)“牛鼻子”,大力發(fā)展新質(zhì)生產(chǎn)力,奮力推進(jìn)華龍一號(hào)實(shí)現(xiàn)“一臺(tái)比一臺(tái)好”目標(biāo)。